A Functional Design Specification (FDS) is the cornerstone of any successful automation project. It details the functional requirements, system architecture, and operational logic, serving as a blueprint for engineers, integrators, and stakeholders.
Whether you’re designing a new control system or upgrading an existing one, a well-crafted FDS minimizes risks, ensures clarity, and aligns all stakeholders.
Engaging an on-demand expert freelancer or subcontractor for developing and writing your Functional Design Specifications (FDS) offers a compelling blend of cost efficiency, specialized expertise, and unparalleled flexibility compared to the traditional employment of a full-time Principal or Senior Control Systems Engineer. This approach not only slashes overhead costs by eliminating the need for benefits, office space, and fixed salaries but also grants access to a global talent pool of specialists who bring fresh, innovative solutions to your projects.
Expert Functional Specifications Writing Services:
Welcome to IACS Engineering, your premier destination for professional Functional Design Specifications (FDS) writing services. With a rich background in Control Systems Engineering and a deep understanding of multi-vendor PLC, PAC, DCS, SCADA & HMI systems, we offer unparalleled expertise to bring clarity, efficiency, and innovation to your projects and it is one of the important Project Management Challenges to be faced by a project manager.
Based on our expert freelancers past experience of writing and developing FDS document and considering relevant industrial standards (Object-oriented features of IEC 61131-3, IEC 61508, IEC 62443, ISA-95, etc), we typically include the following for your deliverable word & pdf copy of the FS document:
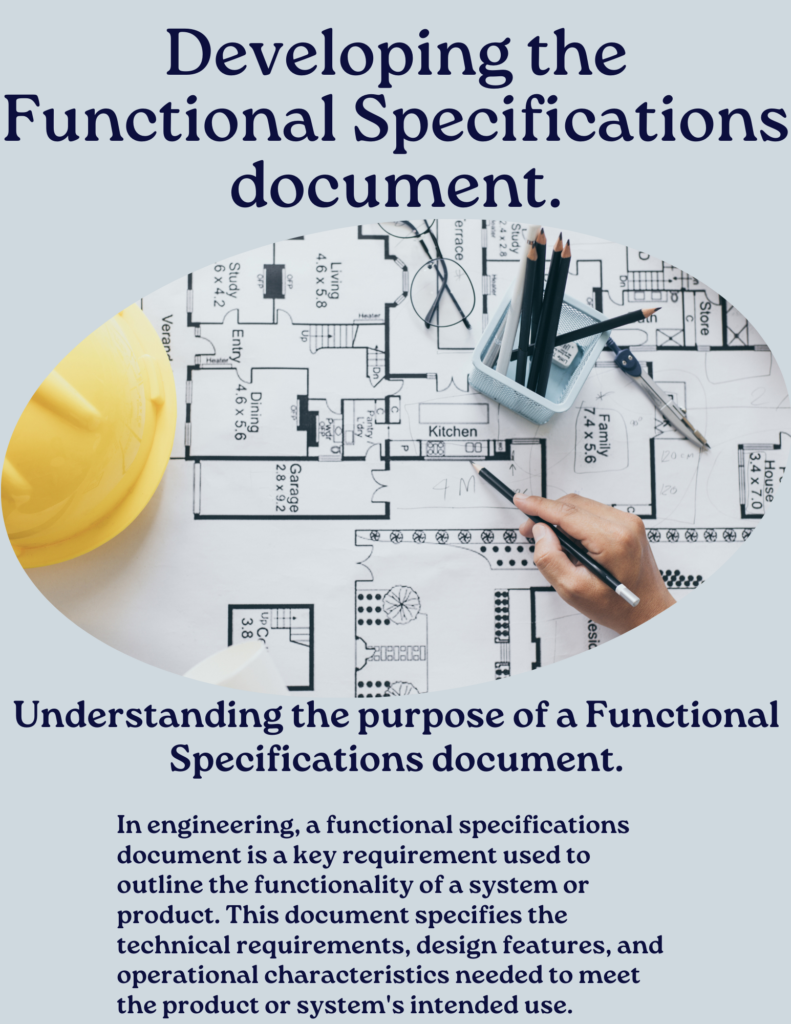
1- System Overview:
- This section provides a high-level description of the entire system, including its purpose, scope, and intended functionalities.
- It may also briefly describe the controlled process and its interaction with the control system.
2- Codes & Standards:
- While the core elements of PLC Functional Specifications remain consistent, international industrial automation and control system standards can influence specific details within the document.
- Here’s a breakdown of how international standards may be reflected:
IEC 61131-3: Programming Languages for Programmable Logic Controllers:
- This standard defines programming languages and associated documentation requirements for PLCs.
- The PLC Functional Specifications should adhere to the chosen programming language’s syntax and conventions outlined in the standard.
- This ensures code clarity, maintainability, and portability across different PLC platforms.
IEC 61508: Functional Safety of Electrical/Electronic/Programmable Electronic Safety-Related Systems (E/E/PESR):
- This standard applies to systems where malfunctions can lead to safety hazards.
- If the PLC is involved in safety-related functions, the Functional Specifications must demonstrate how the PLC program meets the safety integrity level (SIL) required by the application.
- This may involve specific documentation requirements for risk assessments, safety requirements, and verification and validation procedures.
- IEC 60204-1: Safety of Machinery – Electrical Equipment of Machines
- ISO 13850: Safety of Machinery – Emergency Stop Devices – Principles for Design and Selection
Industry-Specific Standards:
- Depending on the application domain (e.g., power generation, chemical processing, material handling solutions, logistics, etc), additional industry-specific standards may apply.
- These standards might impose specific requirements for documentation formats, coding practices, or testing methodologies.
- The PLC Functional Specifications should address any relevant industry-specific requirements for the project.
3- Control System Architecture or System Topology
- This section outlines the hardware components of the system, including:
- PLCs
- HMI/SCADA software
- Sensors and actuators
- Communication networks
- It also describes the system’s network architecture, including communication protocols and data flow between different components.
4- Process Description:
- This section delves deeper into the details of the controlled process.
- It typically includes:
- Process flow diagrams (e.g., flowcharts, P&IDs)
- Description of process inputs and outputs
- Operating conditions and constraints
5- Control Philosophy:
- This section details the overall strategy for controlling the process using the PLC and SCADA system.
- It describes how the system will react to different process conditions and operator inputs.
- Common control philosophies include:
- On/Off control
- Proportional-Integral-Derivative (PID) control
- Sequential control
- Feedback control
- Feedforward control, etc
6- PLC or PAC Functionality:
- Here’s a breakdown of key elements typically included in a PLC & SCADA FDS document:
Permissive:
- Defining Permissive signals to enable safe actions.
Interlocks:
- Defining Interlocks to prevent unsafe actions.
Failsafe Logic:
- Determining failsafe logic and Defining Normally Closed (NC) contact or Normally Open (NO) Contact
Emergency Stops (E-Stops):
- Describing the triggering mechanism for the E-Stop system and safe shutdown sequence, etc.
Modes:
- Auto, Manual, Maintenace, etc.
States:
- Idle, Running, Faulted, etc.
State Transition Diagrams:
- Utilize state diagrams to visually represent the system’s states, transitions between states, and conditions triggering those transitions.
Cause & Effect Diagrams:
- Identifying potential issues early in the development phase, and improving design with enhanced safety considerations.
Modes of Operation:
- Auto, Manual, Maintenance, etc.
Process Cell, Unit, and Equipment State:
- The process hierarchical decomposition.
Control Logic:
- This is the heart of the PLC specification. It details the control logic using a programming language (e.g., Ladder Logic, Function Block Diagrams) specific to the chosen PLC platform. This logic defines how the PLC will react to various sensor inputs, perform calculations, and generate control signals for the connected actuators based on the pre-defined program.
Variable Frequency Drives (VFDs) Motion Profiling, Control & Monitoring:
- Explaining how the PLC/ PAC sends control words to the VFD and receives status words, communication protocol selection or hardwired IOs details for control & status monitoring of the VFDs.
Sequencing and Timing:
- For processes involving specific sequences of operations or requiring precise timing control, this section outlines the sequence steps and timing parameters within the PLC program. This ensures proper order of operations and accurate timing for automated tasks.
Fault Handling:
- This section specifies how the PLC will respond to unexpected events or equipment malfunctions. It may define strategies for identifying faults, triggering alarms, and potentially taking corrective actions within the PLC’s capabilities.
Library of Process Objects Development:
- Maintaining reusable library of process control objects.
Tag Naming Convention – Appendix:
- A consistent and well-defined tag naming convention for referencing specific data points, inputs, outputs, and internal variables and such a convention structure also includes Prefixes & Suffixes.
I/O Mapping – Appendix:
- This section meticulously assigns physical input and output devices (sensors and actuators) to specific memory addresses within the PLC. It ensures the PLC can correctly identify and interact with each connected device.
Communication Protocols Mapping – Appendix:
- This section meticulously assigns physical input and output devices (sensors and actuators) to specific memory addresses within the PLC. It ensures the PLC can correctly identify and interact with each connected device.
7- SCADA Functional Specifications:
The SCADA Functional Specifications document focuses on the functionalities of the Supervisory Control and Data Acquisition (SCADA) system. It outlines how the SCADA system will interact with the PLC, display process information, and provide control capabilities to the operator.
Here’s a breakdown of key elements typically included in a SCADA Functional Specifications document:
- HMI (Human-Machine Interface) Design: This section details the design and layout of the graphical user interface (GUI) for operator interaction. It defines the screens displayed, the information presented (e.g., real-time process data, trends, alarms), and the controls available to the operator (e.g., setpoint adjustments, manual control options).
- Screens & Faceplates Customization: Defining Screen Hierarchy and Standard Faceplate as objects, etc.
- Historical Trending: Standard Historical Trend display screen, default time line, sampling time, etc.
- Data Acquisition and Monitoring: This section specifies how the SCADA system will acquire data from the PLC, including data points, sampling rates, and any data filtering or processing functions.
- Alarm Management Philosophy and Events Logging: This section defines the strategy for managing alarms within the SCADA system. It outlines the types of alarms (e.g., high/low process values, equipment faults), alarm notification methods (e.g., visual on screen, audible alerts), and potential operator actions triggered by alarms.
- Data Logging and Reporting: This section details how the SCADA system will record and store process data. It may define the types of data logged, the storage duration, and functionalities for generating reports based on the collected data.
- Operator Interactions: This section outlines the control capabilities available to the operator through the SCADA system. It may define functionalities like setpoint adjustments, initiating manual control sequences, and potentially acknowledging alarms.
8. Testing and Acceptance Criteria:
- This section defines the procedures and criteria for testing the functionalities of the PLC and SCADA system.
- It ensures the system meets the specified requirements before deployment.
- Testing & Validating Process Objects Library with Process Simulation Objects Library (similar to digital twins)
9. Additional Considerations:
- The FDS may also include:
- Security strategy for the system
- Operator training requirements
- Maintenance procedures
- Future Vision & Scalability
- FAT & SAT Test Sheets
Functional Design Specifications (FDS): Your Blueprint for Automation Success
A well-crafted Functional Design Specification (FDS) is the backbone of any automation project. It transforms complex requirements into actionable engineering plans, ensuring alignment across stakeholders, minimizing risks, and accelerating project timelines.
Why Partner with IACS Engineering for Your FDS?
With 18+ years of experience across industries like power generation, material handling, and chemical processing, our team combines academic rigor (Ph.D., MEng, BEng) and hands-on expertise in multi-vendor systems (Rockwell, Siemens, Schneider, Ignition).
Key Benefits:
✅ Cost Efficiency: Avoid full-time hire overheads—no benefits, office space, or fixed salaries.
✅ Compliance Assurance: Adherence to IEC 61508 (safety), ISA-95 (integration), IEC 62443 (security), and industry-specific standards.
✅ Future-Proof Design: Scalable architecture with reusable libraries of process objects, cutting development time by up to 40%.
Our FDS Development Process
1. Initial Consultation (Free)
We review your project scope, P&IDs, electrical schematics, and I/O lists to tailor our approach.
2. In-Depth Requirements Gathering
Collaborate with our engineers to define:
- Safety Protocols: Failsafe logic, E-Stop sequences, SIL compliance.
- System Architecture: PLC/SCADA topology, communication networks, VFD motion profiling.
- Operational Workflows: Auto/manual modes, state transitions, alarm management.
3. Drafting & Refinement
Receive a structured FDS document including:
- Process Flow Diagrams & Control Philosophy
- IEC 61131-3-compliant code templates
- SCADA HMI Design: Faceplates, historical trends, alarm hierarchies
- Testing Protocols: FAT/SAT checklists, digital twin simulations
4. Final Delivery
Ready-to-implement documents in Word/PDF, validated for global compliance.
Pricing Transparency
- Small-Scale Systems: Starting at $2,500 (fixed fee).
- Complex Projects: Custom quotes with volume discounts for repeat clients.