Evaluating the right industrial communication protocol is crucial for the success of industrial automation and control systems integration projects. These protocols facilitate reliable and efficient communication between various devices and systems, ensuring seamless operations and data exchange. Here’s how to evaluate industrial communication protocols for your projects:
1. Determine System Requirements
- Compatibility: Ensure the protocol supports all devices and systems in your project, including PLCs, HMI, sensors, and actuaries.
- Data Throughput: Assess the volume of data to be transferred and ensure the protocol can handle it without bottlenecks.
- Real-time Needs: If your system requires real-time control, choose a protocol designed for low latency and timely data delivery.
2. Assess Network Topology and Scale
- Topology Flexibility: Consider whether the protocol supports the network topology (star, ring, bus, etc.) that best fits your project’s layout and expansion plans.
- Scalability: Choose a protocol that can scale as your system grows, allowing for the addition of new devices without major overhauls.
3. Consider Protocol Reliability and Robustness
- Error Handling: Look for protocols with strong error detection and correction features to ensure data integrity.
- Redundancy Support: For critical systems, select protocols that support network redundancy to maintain communication in case of a failure.
4. Evaluate Interoperability and Open Standards
- Interoperability: Ensure the protocol facilitates seamless integration with devices and systems from different manufacturers.
- Open Standards: Protocols based on open standards tend to offer greater flexibility and vendor independence, facilitating easier integration and future upgrades.
5. Analyze Security Features
- Encryption and Authentication: Evaluate the protocol’s ability to secure data in transit, including support for encryption and authentication mechanisms.
- Network Segmentation: Consider protocols that support network segmentation to isolate critical systems and reduce cybersecurity risks.
6. Understand Implementation and Maintenance Costs
- Licensing Fees: Some protocols may require licensing fees, so factor these into the overall cost of your project.
- Training and Support: Consider the availability of training for your team and ongoing support from the protocol provider or community.
7. Review Industry Adoption and Support
- Industry Standards: Protocols widely adopted in your industry are likely to be more tested and supported.
- Community and Resources: A strong user and developer community can provide valuable resources and support for troubleshooting and best practices.
8. Perform Testing and Validation
- Pilot Testing: Before full-scale implementation, conduct pilot tests to evaluate the protocol’s performance and compatibility with your systems.
- Vendor Demos: Request demonstrations from vendors to see how their solutions integrate with the protocol and meet your requirements.
By carefully evaluating these aspects, you can select an industrial communication protocol that ensures your automation and control systems are efficient, reliable, and scalable. This selection process is vital for the long-term success of your industrial automation projects, facilitating seamless integration and optimized performance across all components.
With IACS Engineers, you gain a partner with the expertise to navigate the complexities of industrial communication protocols (like Ethernet/ IP, Profinet, MODBUS TCP, EGD, MQTT, etc) , ensuring your automation and control systems are built on a solid, secure, and scalable foundation. Contact us to explore how we can enhance your industrial automation projects through expert consultancy, custom solution development, and comprehensive support services.
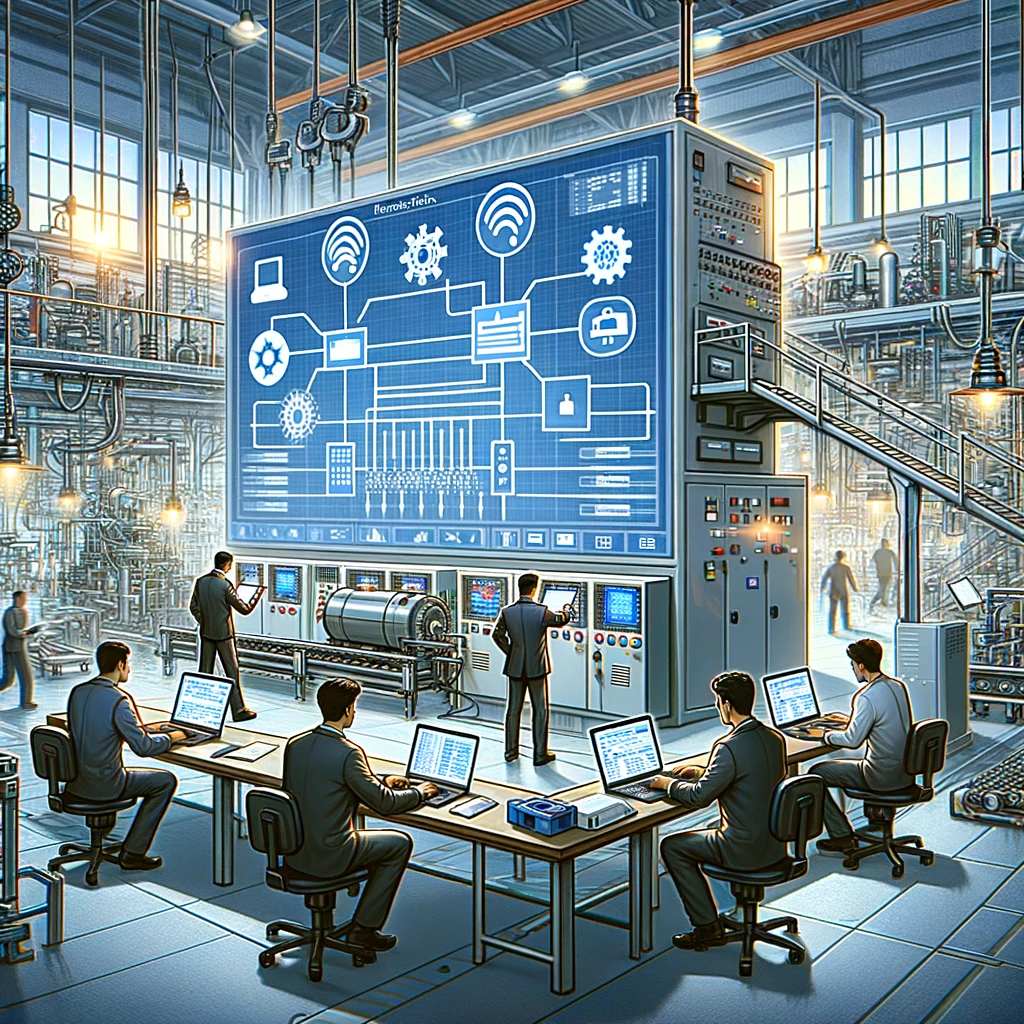