The research overview on digital twins (DTs) and their applications in industrial automation, industrial robots, and industrial control systems showcases the progression and integration of DT technology in enhancing the operational efficiency, predictive maintenance, and innovation within Industry 4.0. Here’s a synthesis of the key insights from the literature:
Security Architecture for Industrial Automation and Control Systems:
- Gehrmann and Gunnarsson (2020) discuss a DT-based security architecture that enhances data sharing and control security for industrial processes. They emphasize the role of state synchronization in DTs for secure software upgrades and outline a framework for future research in DT security.
Comprehensive Review on DT Concepts, Technologies, and Applications:
- Liu et al. (2020) provide an extensive review of DTs, covering concepts, key enabling technologies, and applications across various industrial sectors. They highlight the evolution of DT concepts, the significance of integrating domain-specific expertise, and the potential of DTs in optimizing product lifecycle management.
Real-Time Optimization for Industrial Robots:
- Liu et al. (2023) propose a framework utilizing DTs for real-time monitoring and performance optimization of industrial robots. This includes multi-domain modeling, behavioral matching, control optimization, and parameter updating, demonstrating improved control performance through fractional order control.
AI-Driven DTs in Smart Manufacturing and Robotics:
- Huang et al. (2021) survey the integration of DT and AI technologies in smart manufacturing and advanced robotics. They explore applications ranging from metal machining to human–robot interaction, emphasizing the role of AI in enabling sustainable development through DTs.
DT Framework for Collaborative Robotics:
- Malik and Bilberg (2018) present a DT framework to support the design, build, and control of human-machine cooperation in manufacturing. The framework utilizes computer simulations to create a digital counterpart of a collaborative work environment, allowing for continuous improvements and safer embeds.
Challenges and Future Directions for DT Research:
- Fuller et al. (2020) assess the enabling technologies, challenges, and open research areas for DTs, categorizing recent research by areas such as manufacturing, healthcare, and smart cities. They discuss the integration of DTs with AI and IoT technologies, emphasizing the importance of addressing practical challenges to realize the full potential of DTs.
Experimentable DTs for Process Control and Automation:
- Schluse et al. (2018) introduce the concept of experimentable digital twins (EDTs) that bring DTs to life through simulation techniques. EDTs serve as a basis for simulation-based systems engineering, enabling the creation of comprehensive digital representations for process control and automation.
State-of-the-Art in DT for Industry:
- Tao et al. (2019) review the state-of-the-art in DT research, focusing on key components, development, and applications in the industry. They outline the challenges and potential directions for DT research, particularly in enhancing product design, production, and maintenance processes.
This overview highlights the diverse applications and benefits of DT technology in industrial settings, from enhancing security architectures to enabling real-time optimization and facilitating collaborative robotics. The integration of DTs with AI and IoT technologies is a key theme, underscoring the potential of DTs to drive innovation and efficiency in Industry 4.0.
Transform Your Manufacturing and Production with Cutting-Edge Digital Twin Technology:
Welcome to the forefront of manufacturing innovation! In today’s fast-paced and competitive industrial landscape, staying ahead means embracing the latest in technology. Digital twins represent a groundbreaking approach, offering a virtual model of your physical production plant. Our expert digital twin development services are tailored to help global customers revolutionize their manufacturing processes, ensuring efficiency, precision, and growth.
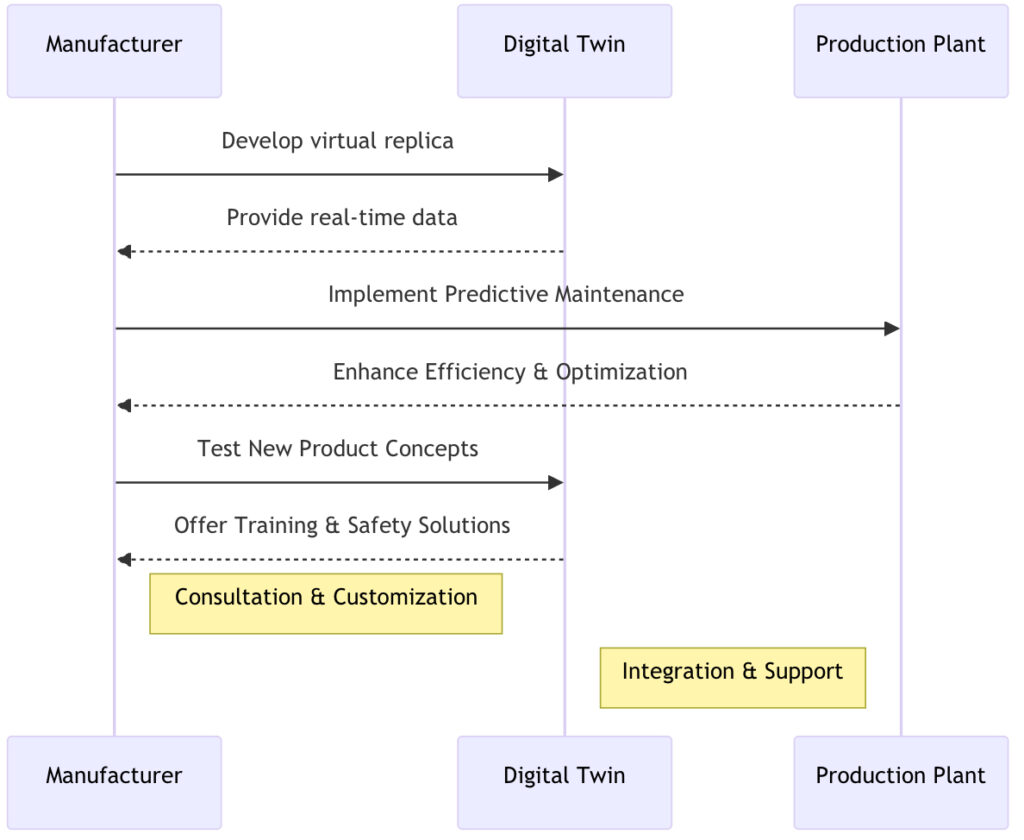
Understanding Digital Twins: Your Plant’s Virtual Concept
Imagine a virtual replica of your entire manufacturing process, accessible at your fingertips. This is what a digital twin offers. It’s not just a 3D model; it’s a dynamic simulation that mirrors every aspect of your physical plant. From individual machines to complex operational interactions, digital twins provide a real-time, comprehensive view, allowing you to test, analyze, and optimize processes in a risk-free virtual environment.
Why Digital Twins are a Game-Changer for Your Production Plant?
Predictive Maintenance:
- Digital twins revolutionize maintenance strategies. By predicting wear and tear, they enable proactive maintenance, reducing downtime and extending the lifespan of your equipment.
Efficiency and Optimization:
- Optimize your operations like never before. Digital twins allow for the simulation of production processes, identifying bottlenecks and enabling enhanced resource management.
Innovation and Product Development:
- Accelerate innovation by testing new concepts in a virtual space. Digital twins facilitate rapid prototyping, reducing the time and cost associated with product development.
Training and Safety:
- Enhance workforce training and safety. Digital twins create a safe training environment, allowing employees to gain experience without the risks associated with physical machinery.
Our Expertise in Digital Twin Technology:
Your Path to a Smarter Plant
Our team specializes in creating bespoke digital twins for manufacturing and production plants. We understand the complexities of your industry and tailor our solutions to meet your unique needs. With our expertise, you’ll gain not just a tool, but a strategic asset that keeps you ahead in the global market.
How We work:
Your Journey Towards a Digital Twin
Consultation and Customization:
- Your journey begins with a comprehensive consultation. We assess your specific needs, processes, and goals to develop a customized digital twin strategy.
Implementation and Integration:
- We seamlessly integrate the digital twin with your existing systems, ensuring a smooth transition and minimal disruption to your operations.
Training and Support:
- Our commitment extends beyond implementation. We provide extensive training and ongoing support, ensuring you maximize the benefits of your digital twin.
Ready to Embrace the Future? Contact Us Today!
Conclusion:
Join the ranks of forward-thinking manufacturers who are leveraging the power of digital twins. Contact us to explore how our digital twin development services can revolutionize your manufacturing and production plant. Embrace innovation, optimize performance, and stay ahead in the global market.
Ready to transform your manufacturing process with a digital twin? Contact us now for a consultation and take the first step towards a smarter, more efficient production plant.